1 引言
随着集成电路制造工艺特征尺寸的持续缩小和互连线内电流密度的迅速增大,如何控制日益严重的由电迁移(electromigration)效应所引起的质量输运,成为超深亚微米铜互连技术中的一个重要问题[1]。大马士革工艺制备的铜互连系统内的质量输运通道包括:体扩散、晶粒间界、铜与扩散阻挡层(Cu/barrier)界面、铜与其上电介质覆盖层之间的界面(即铜线的上表面)等。对原子迁移机制的研究表明,其中最重要的原子输运通道是铜线的上表面[2-3]。通过引入CoWP[4]或Ta[5]等金属性表面覆盖层来阻塞这个最快通道已被证明能够显著的提高铜线的可靠性。然而,在电流改变方向的任何局部区域都会发生电流拥挤,电流拥挤的存在使质量输运路径的确认更加复杂化。局域的电流拥挤不仅能够通过提供一个额外的驱动力来抑制电迁移效应[6],还可能使某些原子输运通道具有更大的原子迁移速率[7]。在本文中,一种专门设计的测试结构可以放大铜/扩散阻挡层界面处的电流拥挤效应,通过对该结构的实验测量和数值分析,我们讨论了铜互连线内电流拥挤对质量输运的影响。
2 实验和结果
采用单层大马士革工艺制备的测试结构如图1所示,包含两段长度分别为150μm的铜线,中间通过3μm长的扩散阻挡层衬垫(barrierliner,BL)来连接。在本文所采用的测试条件下,电子从左侧铜线流入BL,流经整个高电阻的BL,然后进入右侧铜线的阴极端。在电子进出铜线的局部区域,由于电流方向发生变化,出现明显的电流拥挤。因此,在右侧铜线阴极端附近的铜/扩散阻挡层界面区域的电流密度比较高,从而有利于原子沿着这个通道输运。
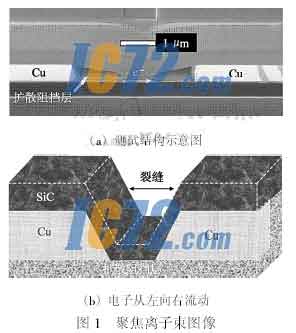
样品的制备方法如下:首先采用标准的单层大马士革工艺来制备铜互连线,经过电镀和平整化的铜线被埋置在600nm厚的SiO2沟槽中,铜线宽度从0.2μm变化到10μm,其上覆盖50nm厚的SiC层作为硬掩模;然后使用宽度为1μm的掩模板和(NH4)2S2O8溶液进行湿法刻蚀,去除长约3μm的铜块,露出铜线下面的扩散阻挡层;最后覆盖一层50nm厚的SiC来钝化表面。该样品结构相当于在铜互连线中出现一个宽约3μm的裂缝,所以称之为S结构。电迁移实验是在晶圆级的探测平台上进行,铜线中心的电流密度为0.45MA/cm2,测试温度范围为105~150℃。
虽然看起来与用于研究质量输运的传统Blech结构[8-9]有些相似,但S结构只需通过将标准的铜互连线刻蚀去除一小段铜块即可得到,故而能够使用标准的25nm TaN/Ta垒层和标准的焊接块(bondpad)。在Blech结构中背应力[8-9] (back-stress)不能忽略,质量输运是电迁移与背应力共同作用的结果;而在S结构中,由于左右两侧的铜线分别连到截面积很大的焊接块(100μm×100μm),所以在右侧铜线的阳极端(即铜线与焊接块相连处)的背应力可以忽略不计,因此S结构能够更直接地反映由电迁移引起的质量输运。
在不同测试条件下,S结构样品的电阻随测试时间而变化的关系曲线如图2所示。由图中可以看出,即使是在用户工作条件下(即环境温度为105℃,铜线中心的电流密度为0.45MA/cm2),仅测试数小时,就可以在所有样品中观察到明显的电阻增大。温度越高,电阻的变化越大;铜线越宽,电阻的变化就越不明显。如果只考虑电迁移效应,根据观察到的电阻变化,可以计算出[10-11]在10μm宽的铜线中,原子的平均漂移速率为16nm/h,扩散激活能为0.73±012eV;而在宽度为3和1μm的铜线中,平均漂移速率分别为49和66nm/h。同时,聚焦离子束(FIB)图像清楚地表明由电迁移引起的空洞首先出现在铜/扩散阻挡层界面处(图3),并主要沿着导线长度方向迅速长大。这些实验结果表明,在S结构中沿着铜/扩散阻挡层界面的质量输运非常灵敏,原子的平均偏移速率远大于相同尺寸的传统Blech结构[11]。
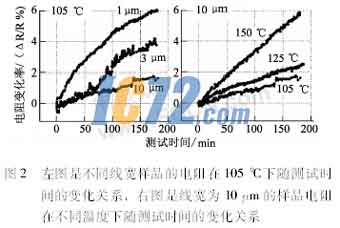
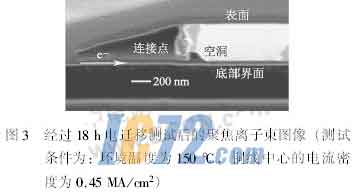
3 分析与讨论
下面我们通过有限元方法来分析和讨论上面的实验结果。
局部原子通量J是由电迁移驱动力产生的,它可由NernstEinstein方程导出并表示为[9]

式中:N代表原子密度;电子电荷e;金属电阻ρ;玻尔兹曼常数k;温度T;Z是表观等效电荷数;j为局部电流密度;D代表原子扩散系数,而D0则是扩散因子;Q是扩散激活能。
三维结构中铜与扩散阻挡层相接触形成底部界面和侧墙界面,其中,沿着铜/扩散阻挡层底部界面的局部原子通量JI,b可表示为[2-3]
式中:下标I代表界面;下标b代表底部;jI,b代表底部界面处的电流密度;δI是界面的宽度;h是铜线的厚度;δI/h则代表通过底部界面输运的原子占所有被输运原子的比例[3]。
为方便起见,取J0=|J0|=|JI,b(j0,T0)|作为计算原子通量的单位;其中j0是Cu线中心(没有电流拥挤的区域)的电流密度,T0是初始温度。如果令Δ|j|=|jI,b|-|j0|和ΔT=T-T0,那么当ΔT<<T0时可以由公式(1)和(2)得到
而因底部界面扩散引起的局部原子通量散度(J/r)I,b,则可以根据下式由电流梯度(j/r)I,b和温度梯度T/r计算得到[12]
在这里取(J0/nm)为原子通量散度的单位。公式(4)描述了局部电流密度分布和温度分布对原子通量散度的贡献。
电迁移引起的质量输运是受局部电流和温度所驱动。然而,直接测量电流密度和温度的分布是非常困难的。幸运的是,三维的热电耦合有限元分析能够模拟出互连系统内部的电流拥挤和温度分布。电流密度分布的计算只需进行稳态分析即可,然而温度分布会随着热传导性能的不同而显著变化,所以热学分析要复杂得多。由于在实际样品制备过程中不可避免地存在不同程度的局部污染以及不同材料之间的附着或接触不良,这些因素会显著地影响热传导性能,从而导致即使在完全相同的测试条件下,每个样品内部的温度分布都可能不同。两种极端的情况是:理想状况下,热从测试结构传导到衬底的效率非常高,以致于在测试结构内部不可能出现任何明显的局部温度变化,电流所产生焦耳热的
影响可以忽略;与之相反的是最坏情况,测试结构与周围材料间的热传导系数非常小,电流会在连接左右两侧Cu线的BL上所产生的焦耳热,进而在Cu线内引起相当大的温度梯度。实际状况介于这两种极端情况之间。
扩散阻挡层衬垫(BL)与右侧铜线连接点附近的电流和温度分布如图4所示,模拟计算所用的条件为:电子从25nm厚的BL流入1μm宽、450
nm厚的铜线,铜线中心的电流密度等于0.4MA/cm2,环境温度为105℃,取铜/扩散阻挡层界面宽度δI≈0.5nm[9]。上述两种极端情况下铜线内与连接点相距0.5nm处的有限元分析结果在表1中列出。虽然局部电流密度在铜线中心为0.4MA/cm2,但是由于电流拥挤效应,从表1第2行可以看出,在距离连接点0.5nm处则高达11.8MA/cm2,增大了约30倍,这使得局部的电流密度梯度高达0.6MA/(cm2·nm)。根据公式2,3,4,可以估算出表1中所列的沿铜/扩散阻挡层底部界面输运的局部原子通量和通量散度。即使不考虑温度梯度的作用,电流拥挤效应也足以将连接点附近的原子通量增大30倍。
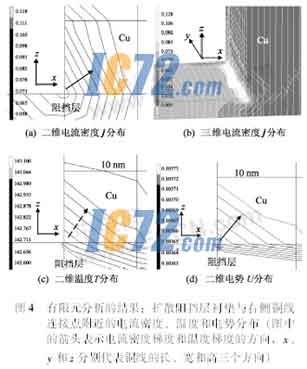
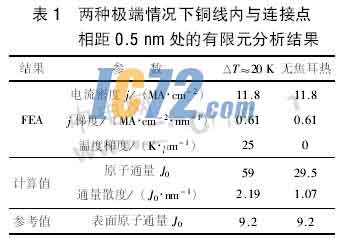
从表1还可以看出,由于连接点附近的电子集中沿着铜/扩散阻挡层底部界面流动,铜/扩散阻挡层底部界面处的局部原子通量远大于铜线上表面处的原子通量(9.2J0)。再加上铜/扩散阻挡层侧墙界面的贡献,这就解释了为什么在该测试结构中铜/扩散阻挡层界面是比铜线上表面更高效的快速原子输运通道。对于较宽的铜线,还必须考虑在电流拥挤区域沿晶面间界的输运,但在S结构中不太可能检测到。
下面来讨论焦耳热的影响,电流产生的焦耳热主要局限于S结构中的BL区域。计算表明(表1第3列),最坏情况下BL与右侧铜线连接点的温度约升高20K,局部温度梯度高达25K/μm,局部原子通量和通量散度都约为理想状况时的2倍。因此,在介于两种极端情况之间的实际状况下,取决于测试结构的热传导效率的不同,焦耳热会使原子通量和通量散度增大到理想状况时的1~2倍。与电流拥挤效应相比,焦耳热及其产生的温度梯度对质量输运性质的影响是有限的。在空洞形成并长大的过程中,电流拥挤效应和焦耳热同时起作用并相互增强,最终导致沿着铜/扩散阻挡层界面发生显著的质量输运。以上实验和分析结果表明,高度局域化的电流拥挤能够影响各种原子输运通道的效率,在尺寸更小的先进互连系统中,这种现象可能使互连可靠性问题更加严重。
4 小结
总之,本文研究了一种专门设计的测试结构中电流拥挤效应对电迁移的影响。有限元分析得到的电流和温度分布表明,由于电流拥挤效应,在用户温度下沿特定通道输运的局部原子通量增大30倍。在未来的互连系统中,因为互连线尺寸的继续缩小,相应的电流密度剧烈增长,可以预期电流拥挤效应将更加显著,它对电迁移和质量输运的影响将不能忽略。 |